SAVE MONEY WITH AIR
Inhale, exhale – we fill our lungs with oxygen with around 20,000 breaths of air each day. By comparison, a laboratory “breathes” significantly slower: fume hoods suck air out, and the ventilation draws fresh air back in. While that makes things safe, it also consumes a huge amount of power. Controlled by a clever air management system, however, more energy – and therefore money – can be saved than some might think.
Makes sense to focus on efficiency
Ultimately, we breathe more under exertion than during day-to-day activities, and breathe less at night. Our breathing rate and air volume is perfectly tailored to our oxygen needs. As much as we need, and as little as possible: the same is true for the laboratory air management system.
In short, how can the extract air system extract only as much air as is necessary via the fume hoods while preventing the room air being contaminated with harmful substances? After all, the safety of the personnel is the top priority.
At the same time, how can they consume as little energy as possible, for example by mirroring the human respiratory system and tailoring the supply of air to demand? To illustrate, a standard fume hood consumes around as much energy as a two to three family homes each year with continuous laboratory operation. That’s as though we're breathing the whole time, as if we’re doing sport. The ventilation and fume extraction of a laboratory, then, is a decisive cost factor in operating costs. It therefore makes sense to focus on efficiency.

Waldner motion sensor
Controllers ensure efficiency
For 40 years, Waldner has not just developed ever more efficient fume hoods such as the Secuflow fume hood with sophisticated flow technology, which consumes 33% less air than standard fume hoods. “Few realise that we have been producing the air flow dampers necessary to do this for decades”, says Bernd Schoeler, Product Manager in Laboratory Solutions. “We’ve even developed a patented measurement technology to regulate air flow, because the more precise the measurement, the better the air volume can be dosed.”
The controller automatically sets the air flow volume – for example, depending on how far the vertical or horizontal sash of the fume hood has been opened. The more open it is, the more air the fume hood has to extract from its work area to prevent harmful particles being released into the air. From an energy point of view, on the other hand, it also makes sense to reduce the air flow rate again as soon as possible.
This is where an additional sash controller comes in. Bernd Schoeler explains: “Its motion sensors detect when no-one is near the fume hood any longer, but the sash is still open. The energy effect of such a situation is comparable with the heating being turned on while the windows are wide open for hours on end. Once the controller detects this is the case, it automatically closes the sash and the air flow damper reduces the air flow volume again.”
Because Waldner is the sole manufacturer, and produces the right controller for its own fume hood, both components are optimally tailored to each other. As a result, this too saves energy. Not only this, but under the required EN 14175 Part 6 type examination, they form an inseparable unit and are awarded the corresponding declarations of conformity. That saves customers coordination costs, and means they only need one point of contact in the event of a warranty claim: Waldner.
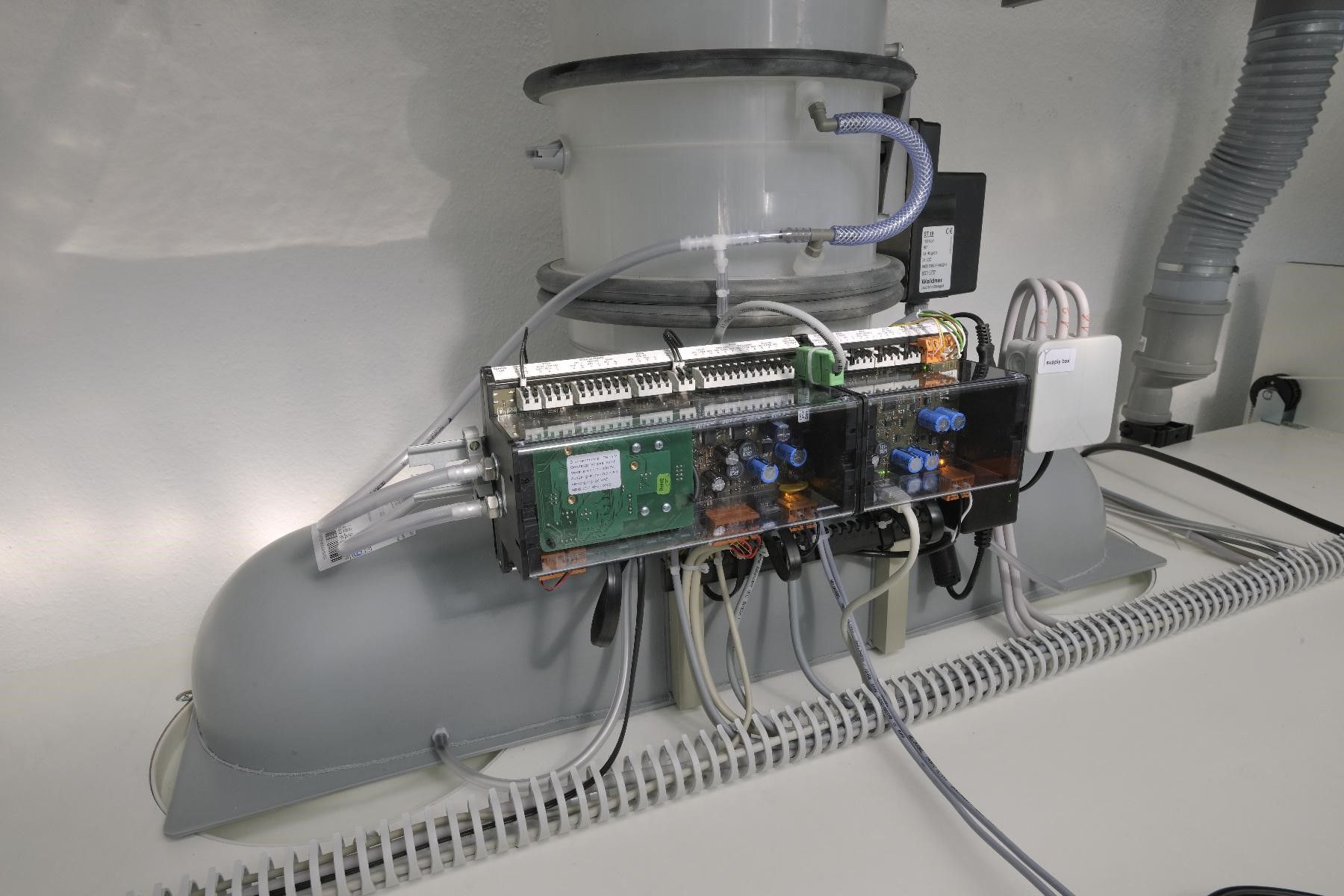
Waldner control unit
Control system offers even greater efficiency
But the efficiency doesn’t stop there – by employing just one control system for the entire laboratory, all the fume hoods, air flues, local extraction systems and extraction cabinets can be coordinated with each other. Ultimately, it's about regularly replenishing all the air in the laboratory with fresh air for the safety of the people working there. The Federal Institute for Occupational Safety and Health (Bundesanstalt für Arbeitsschutz und Arbeitsmedizin, BAUA) requires that 25 cubic metres of air be replenished every hour for every square metre of laboratory area. In a standard laboratory with a height of three metres, that corresponds to around an eight‑fold air exchange rate.
“A configuration may look as follows: If only three of five fume hoods are in continuous operation, these will be operated with higher extract air volumes in order to achieve the required room air exchange”, explains Bernd Schoeler. However, their power can immediately be reduced as soon as the other two also come online. This means the overall safe air flow rate remains the same without becoming excessive. It’s about ensuring the overall balance of extracted laboratory air and automatically replenished fresh air.”

Waldner fume hood test
Savings of at least 35%
The air flow rates of all fume hoods can also be adjusted to working times. At the end of the working day, a four-fold air exchange is sufficient, and the air flow rate reduces to up to 100 m3/h. Compared to 24 hour operation, these measures alone mean savings of at least 35%, depending on the fume hood size. But it goes further than that: with the sash closed, for example, the fume hood can power down to 200 m3/h in Standby mode during working hours – saving even more energy. By comparison, the maximum air flow rate can be up to 330 m3/h even with a small, economical, 1200 mm Secuflow bench-mounted fume hood.
Better performance with the Waldner air management system
The firm Zeller+Gmelin GmbH & Co. KG from Eislingen/Fils were also impressed by the developed air management concept. In 2015, the company not only tasked Waldner with equipping a new quality and control laboratory at its subsidiary Südöl, but also with its air management system. “Using the BACnet IP communication protocol, we were able to integrate it easily into our building management system”, according to Daniel Knospe, Head of Plant Technology at Zeller+Gmelin. The building management system (BMS) only takes care of the basic controls – ventilation on or off – while the Waldner system takes care of all the fine tuning. “We’ve had very good experiences with it. The performance was significantly better than in our laboratories where the BMS also took care of the laboratory air management.” The perfect coordination of fume hoods, controllers and the overall Waldner control system is clear to see.

Sash closing
Good solutions thanks to early involvement
The company’s experiences with the system were so good that Waldner was tasked with equipping another laboratory measuring 164 m² in 2019, including installing the air management system, and a third laboratory is even scheduled for this year. “Each laboratory has different needs and equipment”, says Bernd Schoeler, “we have a solution for almost any situation, allowing energy-optimised operation.” Daniel Knospe concurs: “I was surprised by Waldner’s innovativeness. We had various special requirements, which the engineers were able meet using tailored solutions.” He states that a great deal of expertise was required even before the order was placed. “During this process, it’s about finding the best solutions, and then placing the order. It’s about being willing and able to drill down to the details to deliver a tailored solution”, stresses Daniel Knospe. He is impressed by the planning engineers’ work.
Bernd Schoeler is pleased with the feedback, and agrees: “Only when our customers involve us so early in the planning phase do we have such freedom to implement their needs and ideas. And our customers are often surprised that we have even anticipated many of their ideas beforehand.” This is thanks in no small part to the experience of the Waldner engineers, who have been implementing the widest range of efficient air management solutions for decades.